Song JY, Vrana D, Heo S, He X, Shim J. Snap-interlock module system: Exploring an alternative architectural construction method. International Journal of Space Structures. 2023; https://journals.sagepub.com/doi/10.1177/09560599221147468
stack-interlock
SIMS (Snap-Interlock Module System)
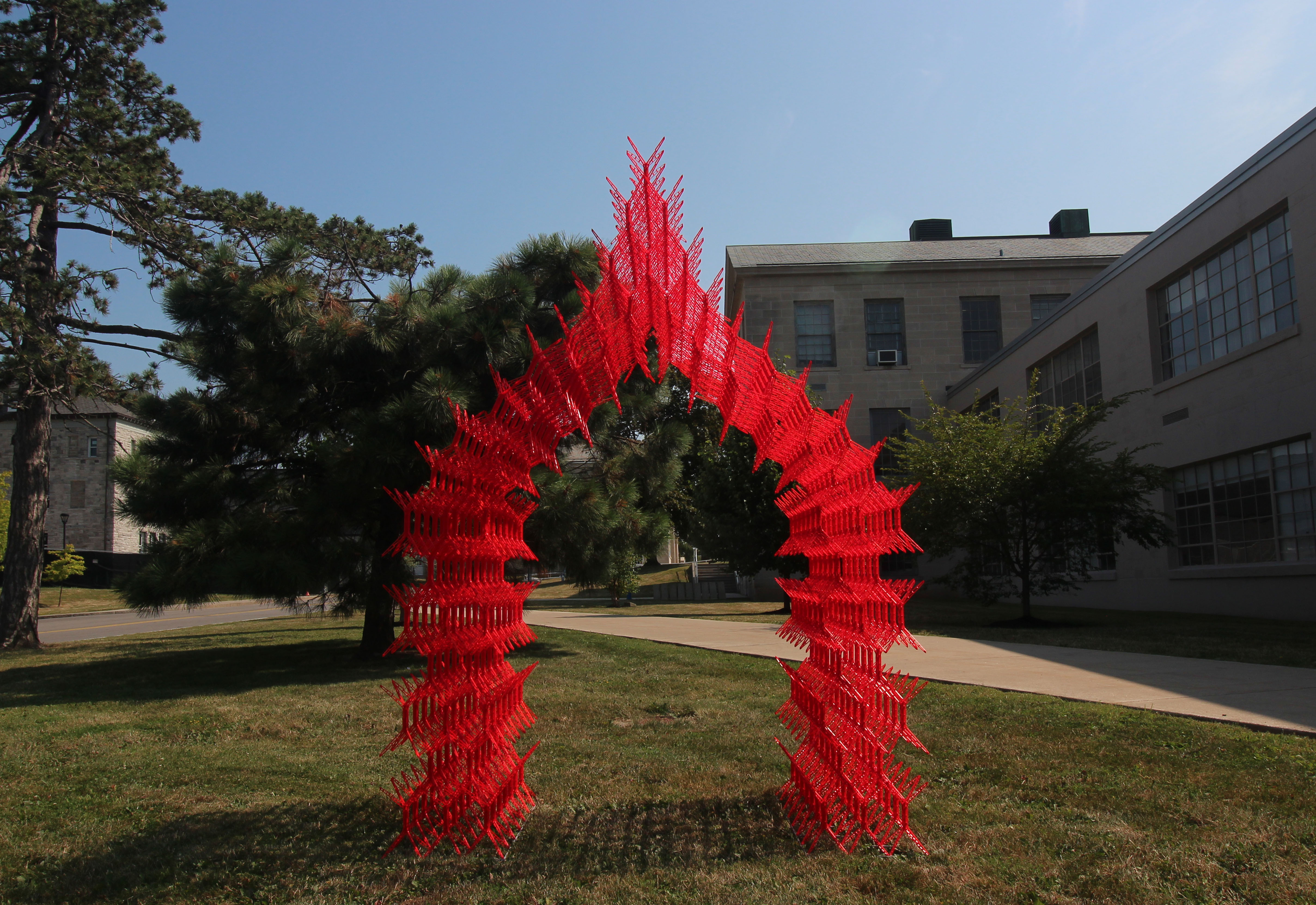
SIMS Prototype test (Image by Jin Young Song)

SIMS prototype (Image by Jin Young Song)
SIMS (Snap-Interlock Module System) is a structural module prototype based on the elastic instability of steel, distributing forces through its unique stacked and interlocked mechanism. One module has 4 hooked legs in the top and bottom direction, when one module snaps into 4 legs from connecting 4 modules, the 5 modules are interlocked as one unit. Finite Element analysis shows the elastic nature of steel and confirms the structural integrity for the construction scale. The module can be cast or cut to assemble for mass production. The internal structure of the module can be controlled to increase the stiffness. The center connector can be added to allow specific angles to form a curved geometry. The snap-interlock stacking is relatively easy to do by human hands and two arch shape prototypes are built using 3d printed modules. The system can achieve limited geometric freedom. Despite further structural analysis and new interpretation necessary, this ‘part to whole’ system can be applied to the building structure, facade application as sub-structure, sheer wall, partition wall, and more.

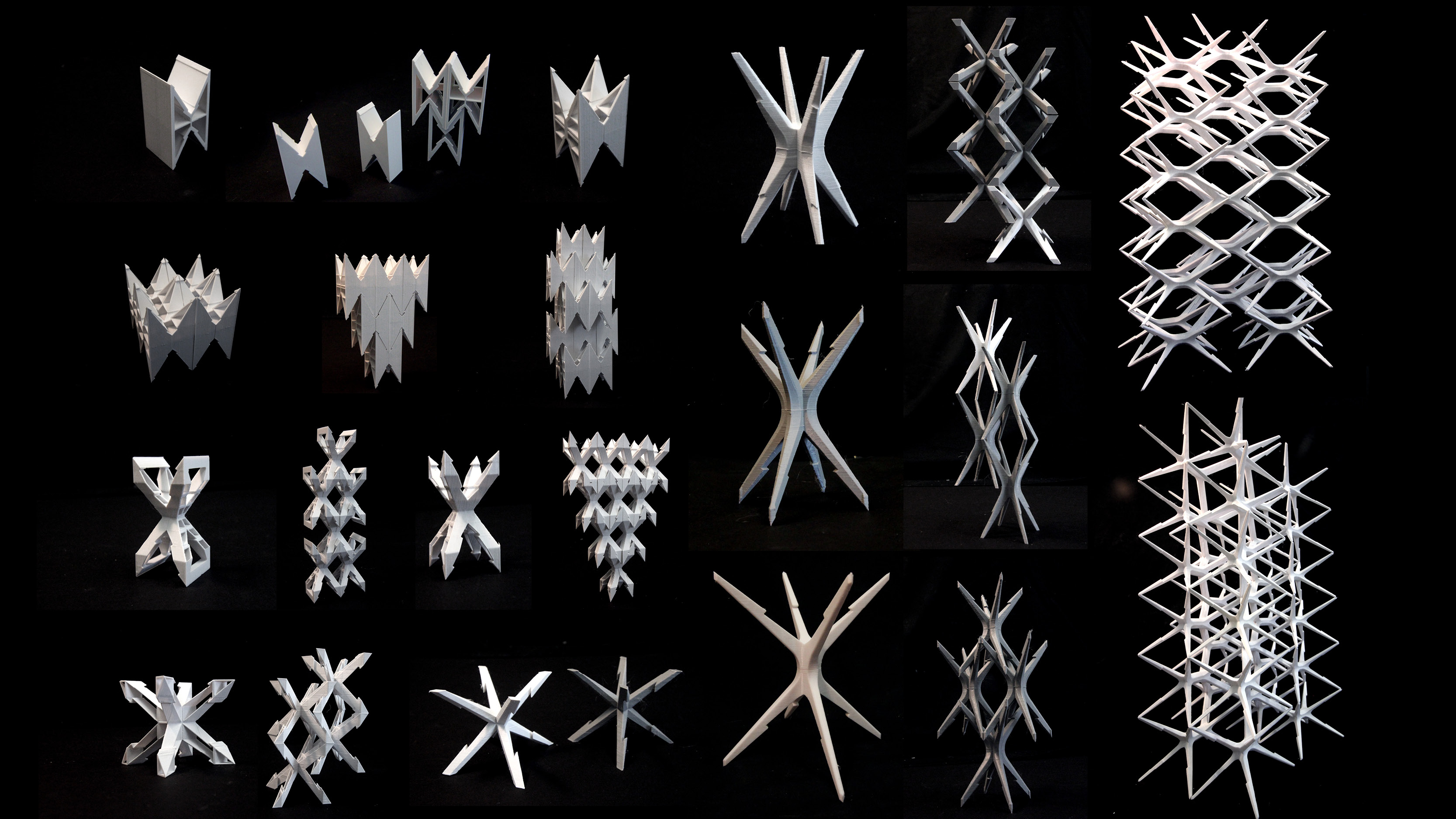
SIMS module studies (Option 1-26) (Image by Jin Young Song)

SIMS module studies (Option 25) (Image by Jin Young Song)

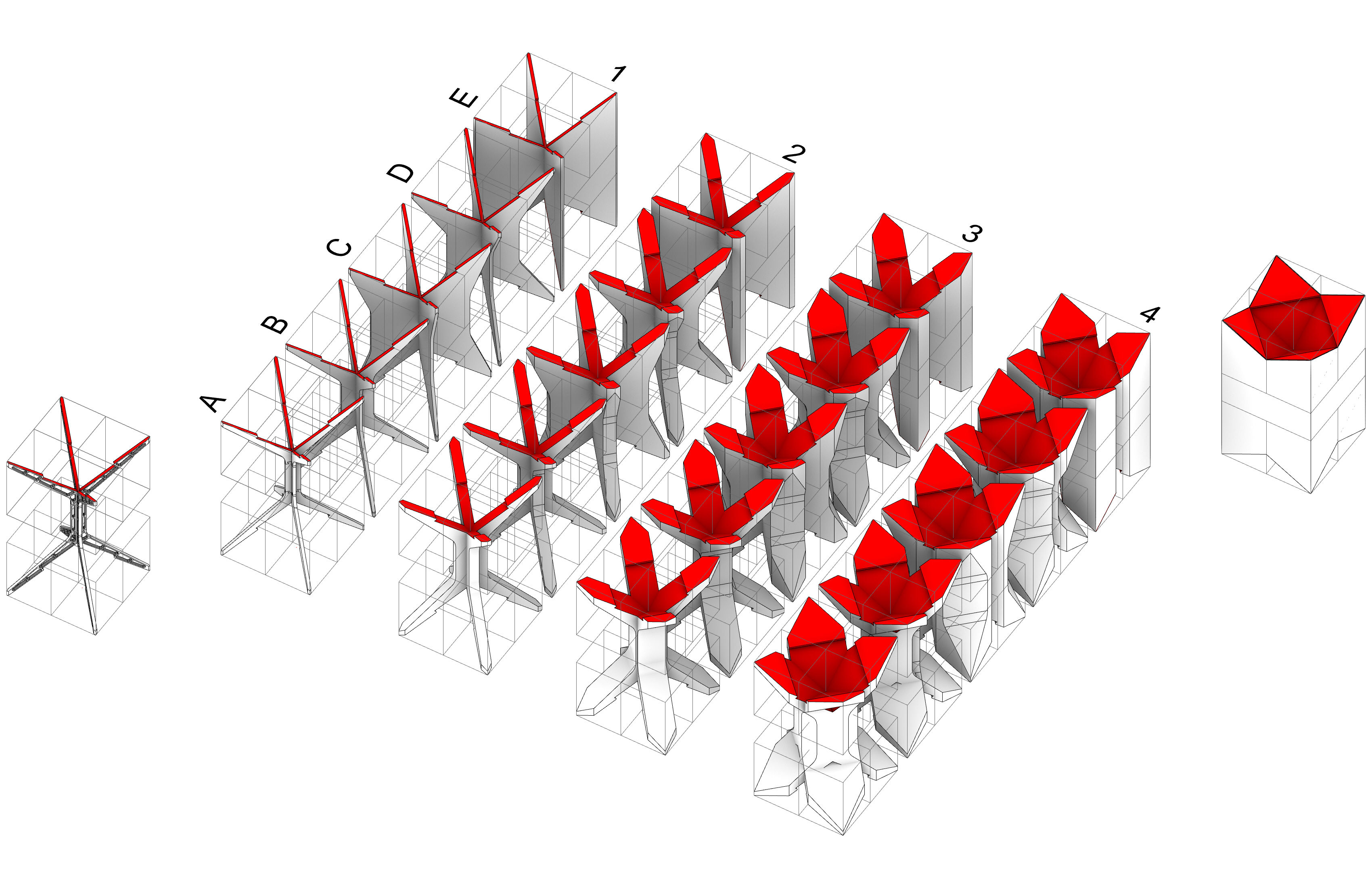
Web-plate diagram of SIMS module (Image by Jin Young Song)
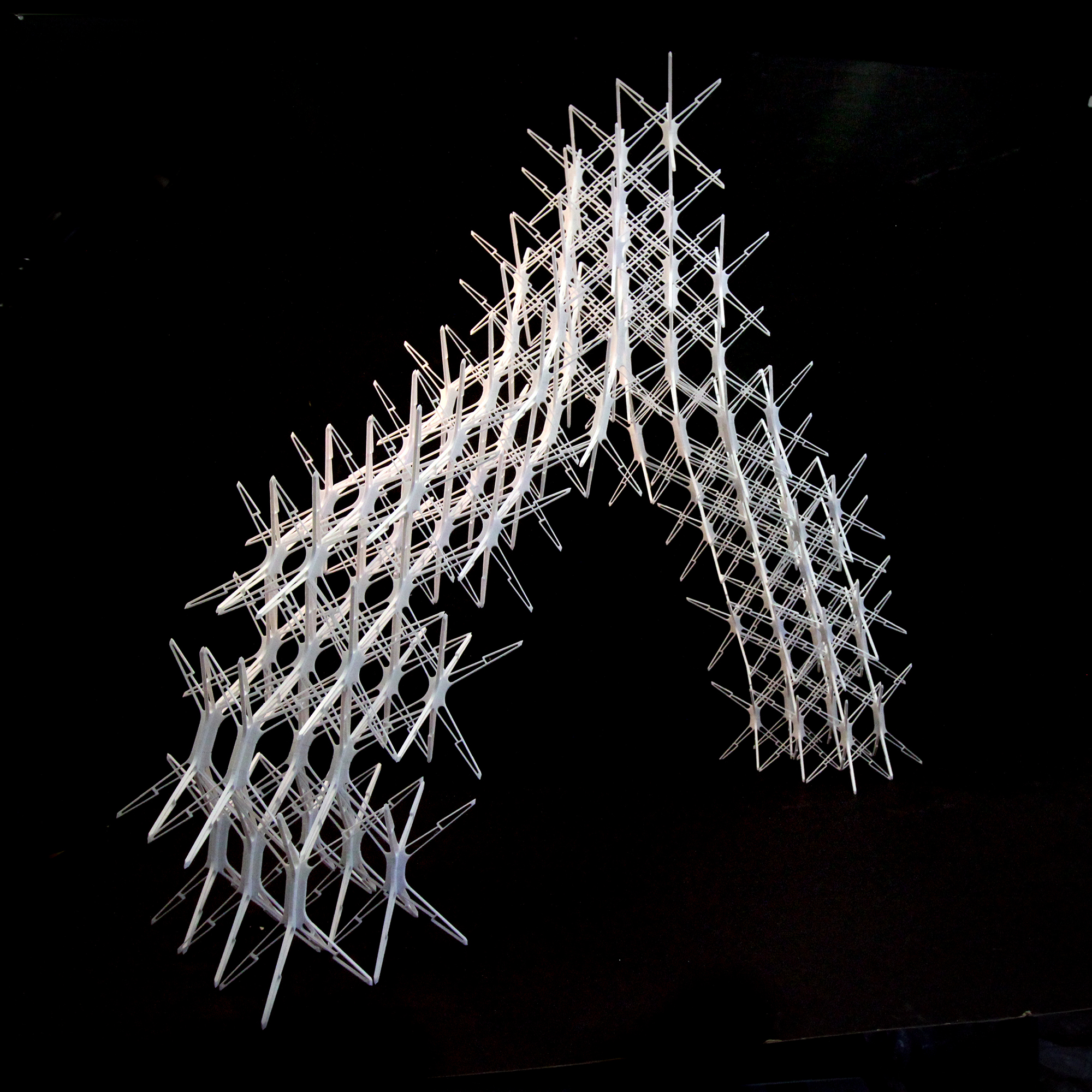
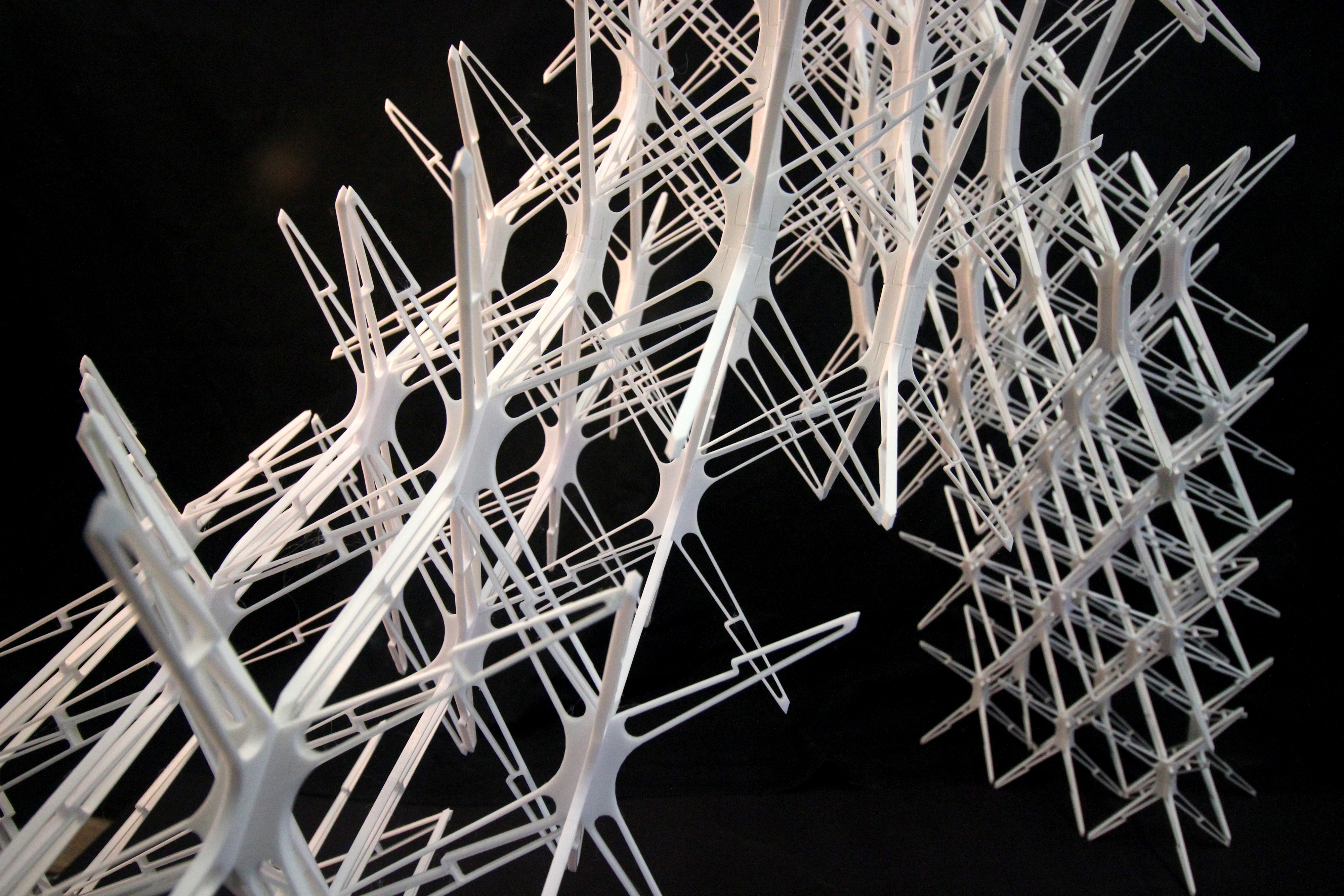

Rendering of SIMS prototype
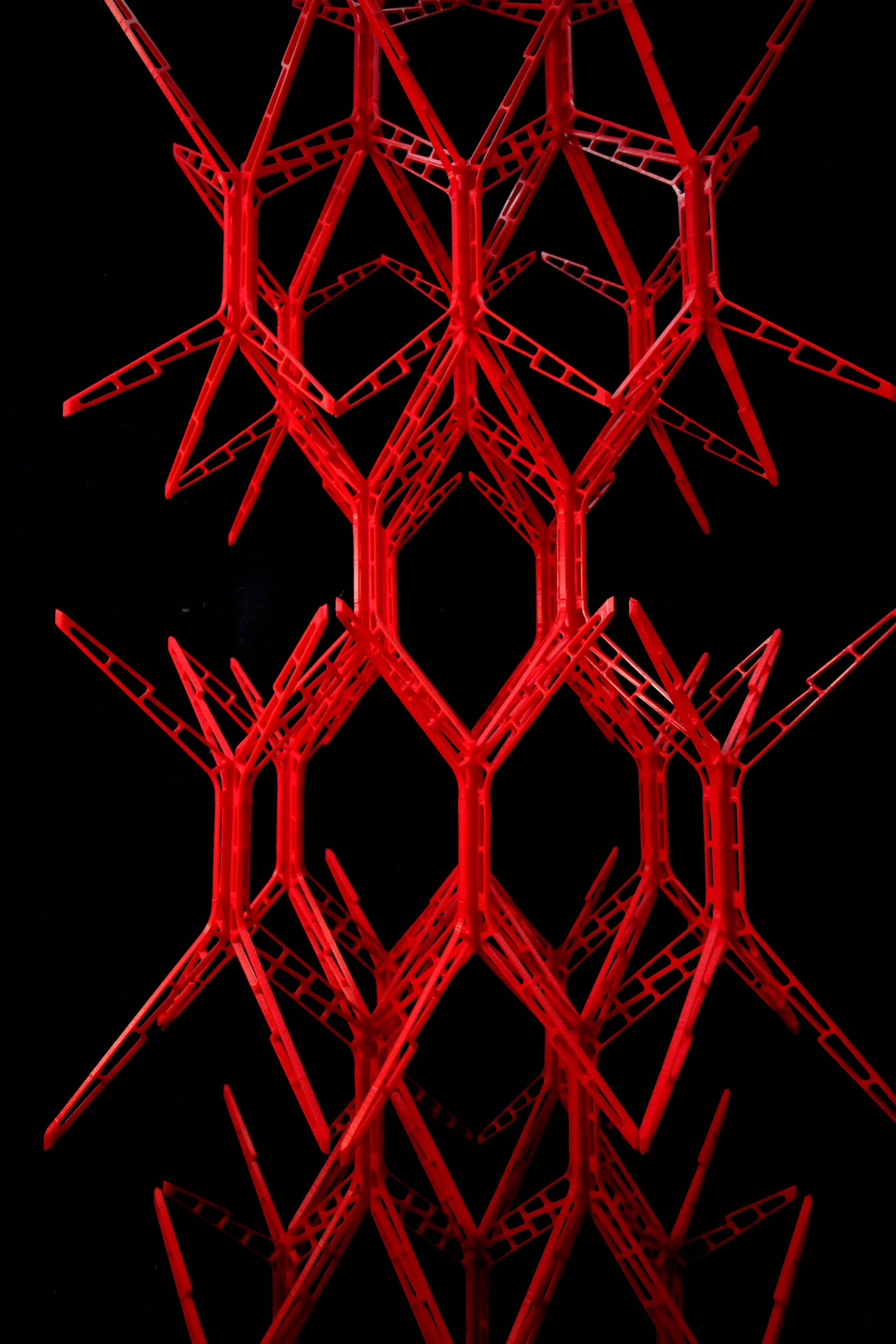
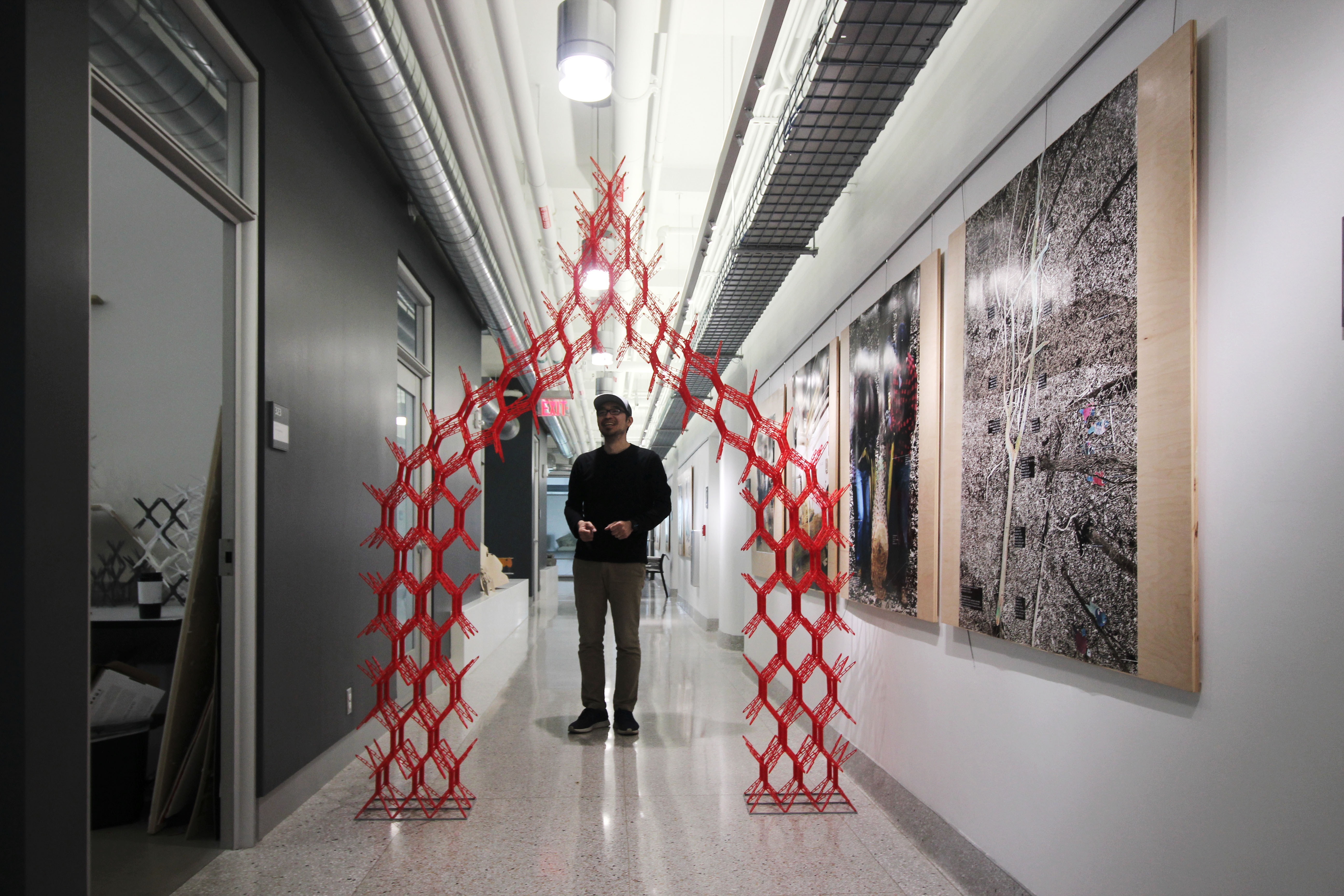
(Image by Jin Young Song)

Steel sheet OMAX Waterjet cutting (Photo by Dan Vrana)

Process of stacking using waterjet cut module (Photo by Dan Vrana)

3d printing and Waterjet cutting of steel:
The project involves with innovative fabrication method to achieve geometric freedom. Keeping coordinated modular property of the SIMS modules, the geometry of the center joint can allow the organic growth of this ‘part-to-whole’ system. We acknowledge the growing potential of the additive manufacturing and as we test printed the modules with the support from Buffalo Manufacturing Works, it opens up unlimited flexibility in shaping the geometry. It provides great benefits for customizable iteration of pieces with exceptional strength, even though we have less understanding of the stress analysis comparing steel sheet legs versus 3d printed steel joints. We are learning about the time of the printing, cost, and the necessary process of post-processing. On the other hand, aiming for the market product and more ‘intimate’ use of steel, the project searches for a simpler and faster way to fabricate the 3-dimensional pieces too. The team tested 5 axis Omax waterjet cutting, carefully controlling the angled faces. This allows precise cutting and a wide range of angled cutting for 3 dimensional needs (See the movie clip below).
Waterjet cutting simulation
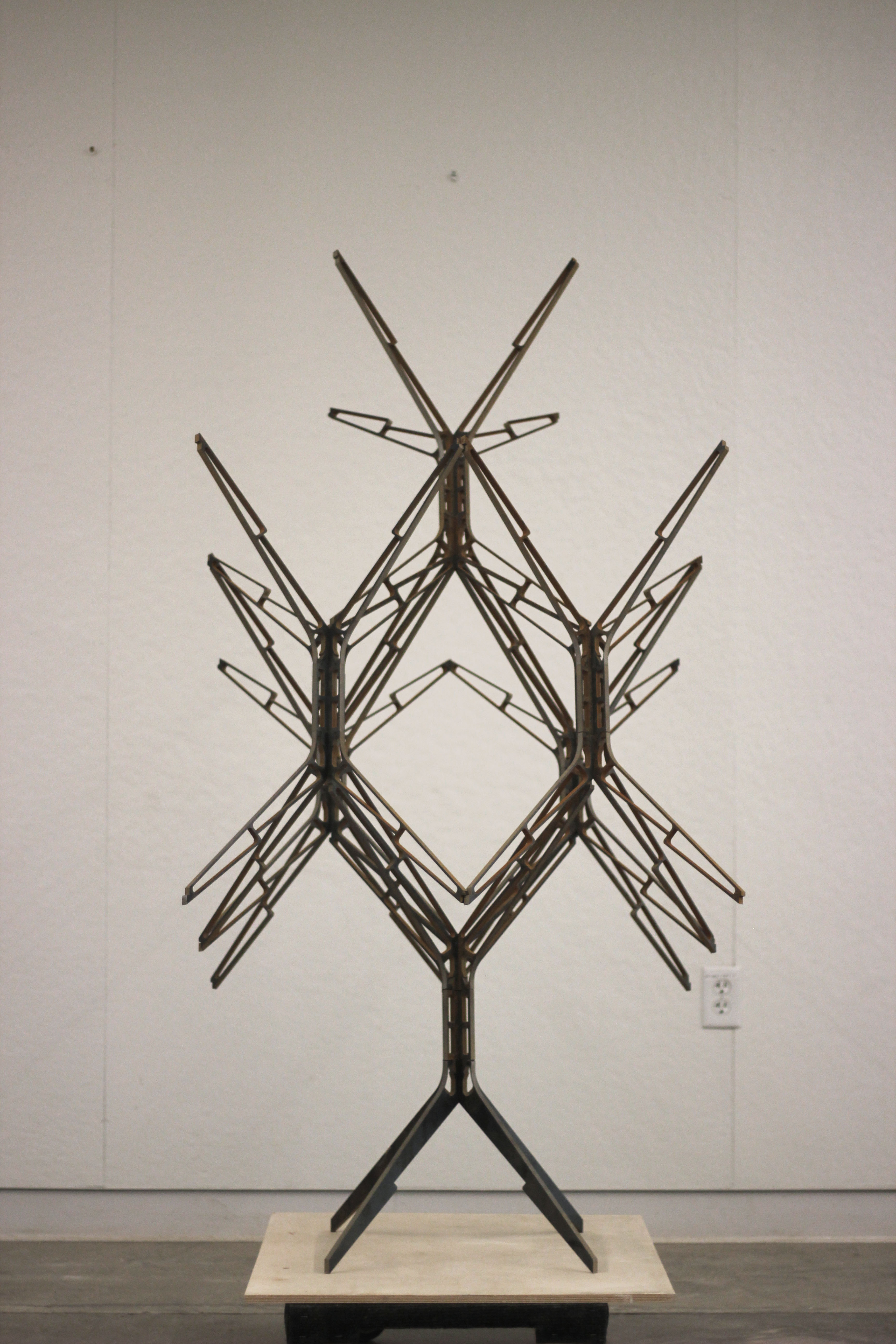
Full size SIMS prototype cutting steel sheet
(Image by Jin Young Song)
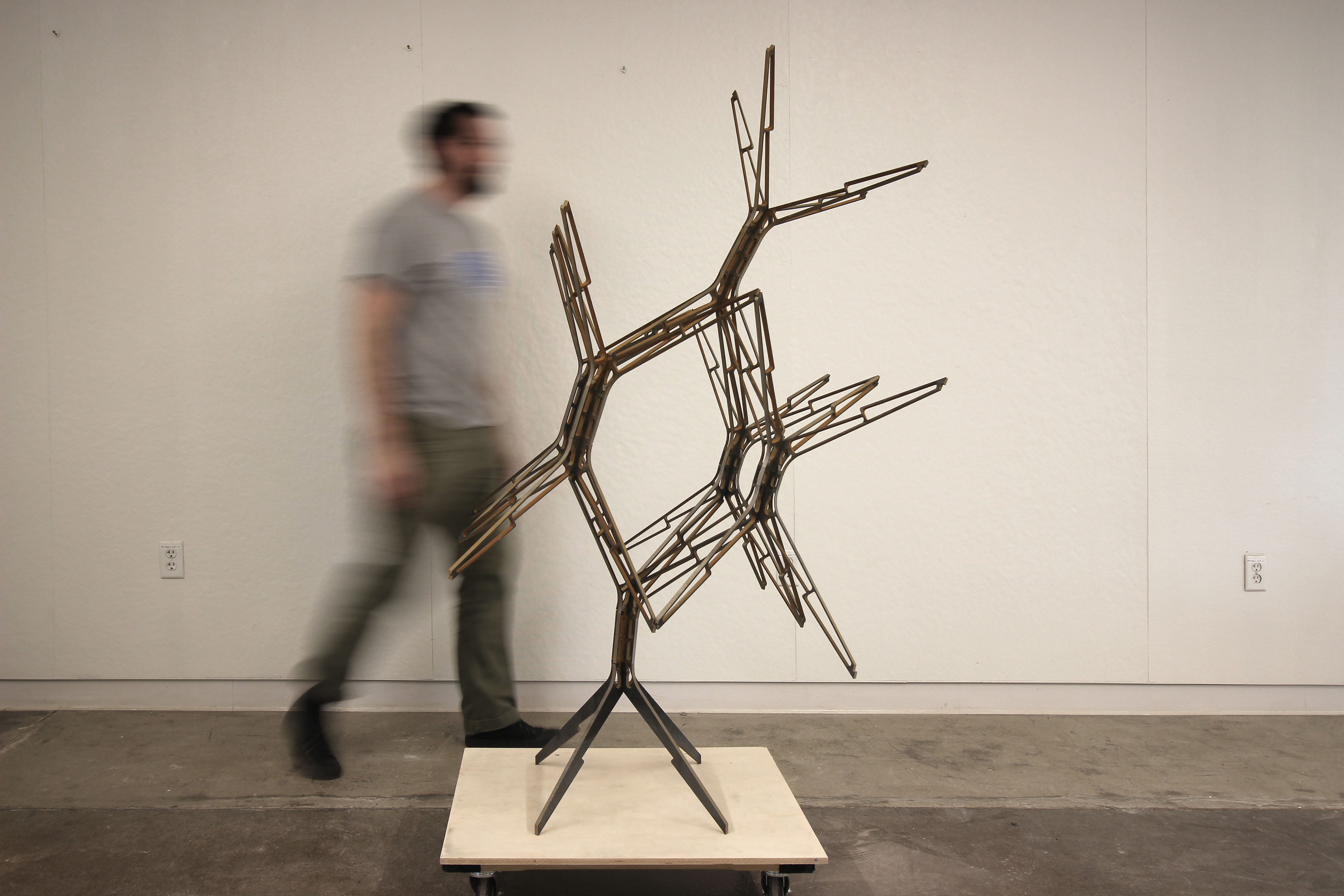
Full size SIMS prototype cutting steel sheet
(Image by Jin Young Song)
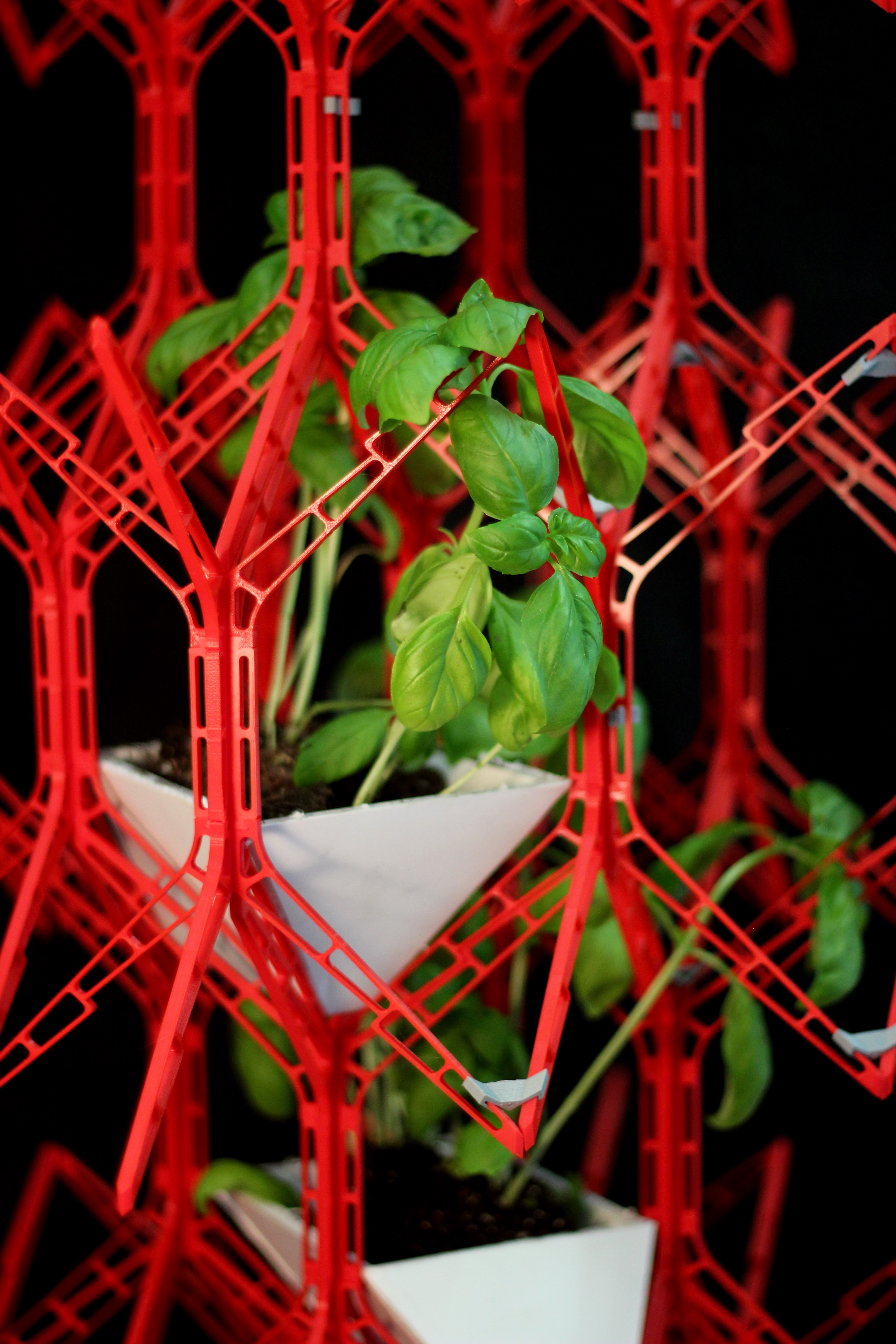
SIMS application for customizable vertical green wall
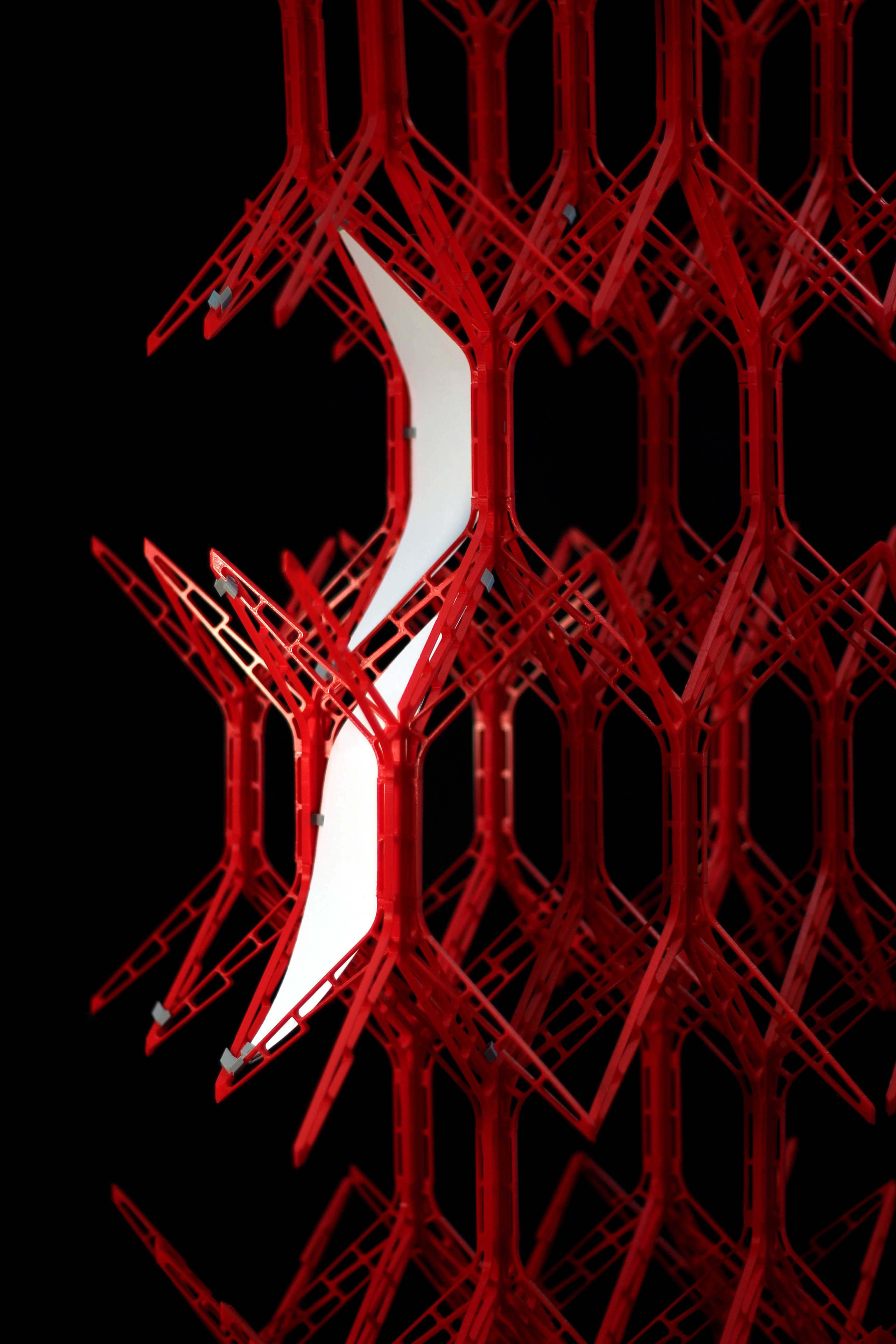
SIMS application for rain screen (facade application)
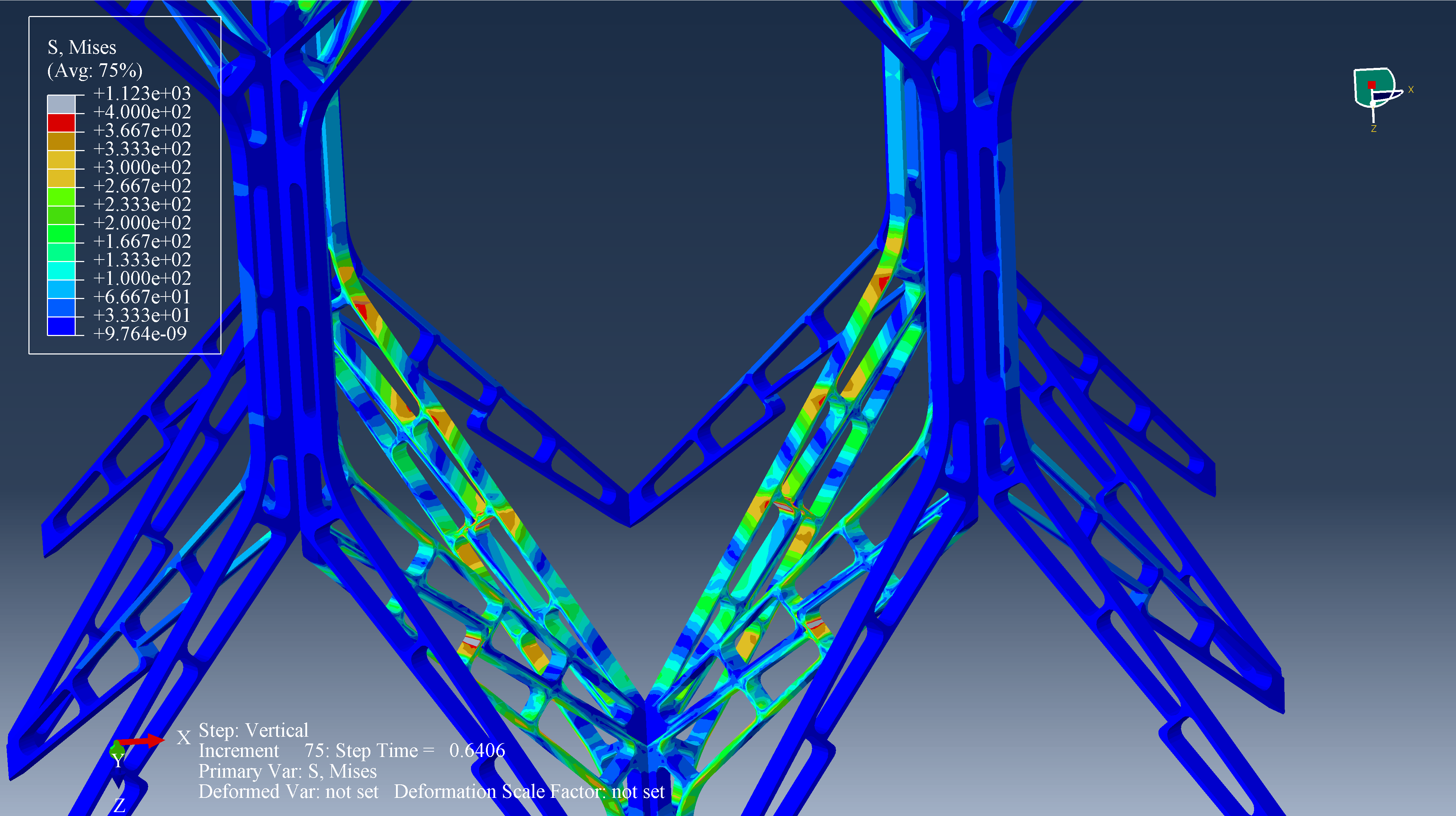
Finite Element analysis of SIMS prototype (Image by Jongmin Shim and Xiangdong He)
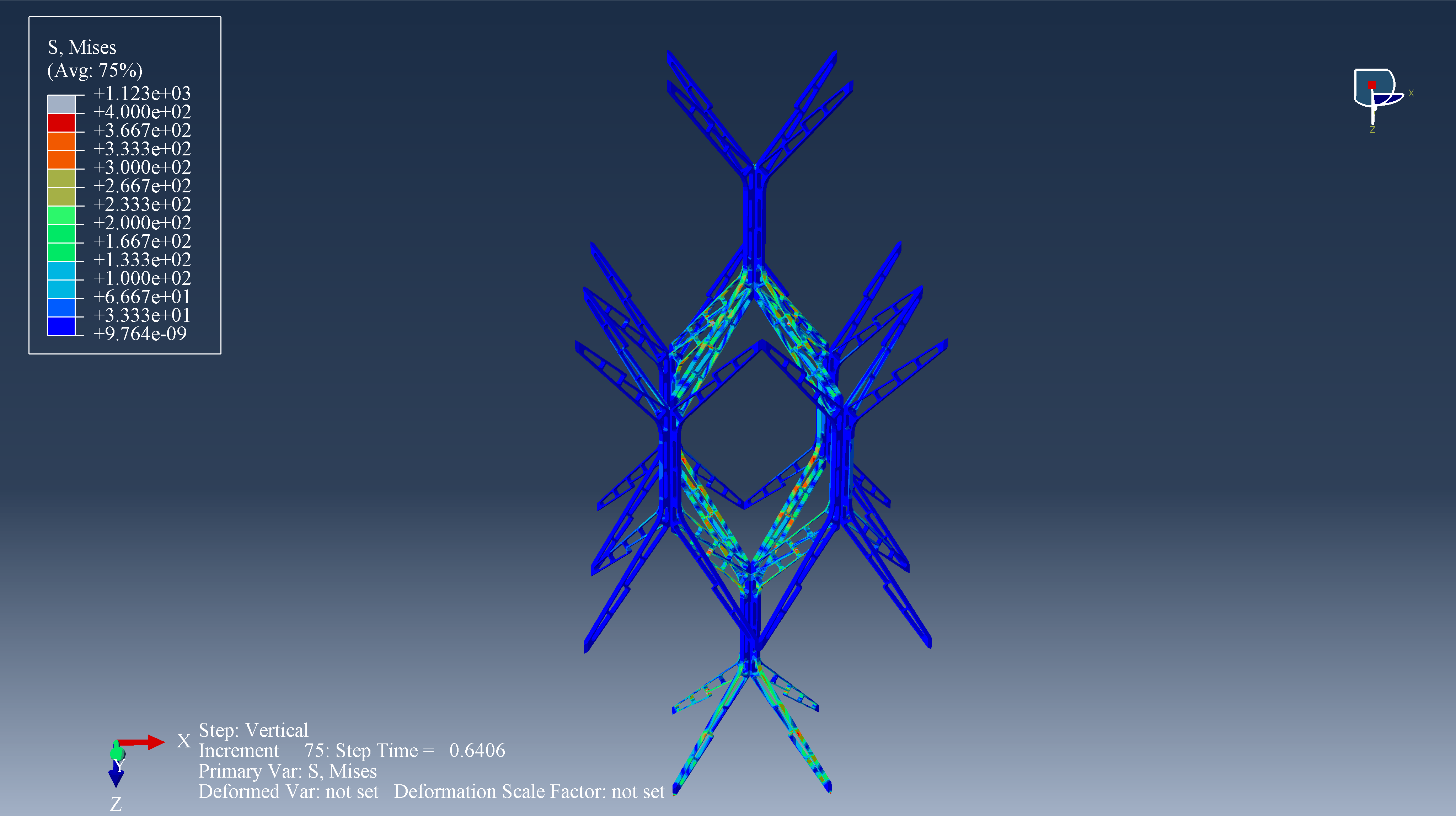
Finite Element analysis of SIMS prototype (Image by Jongmin Shim and Xiangdong He)
The SIMS prototype (Figure 1) can be packed into one typical suitcase.
SMART Convergent Conversation (3/13)
Forge Prize Phase 2 presentation (5/29)
TEAM:
Jin Young Song
Assistant Professor, Department of Architecture
University at Buffalo
Dan Vrana (Fabrication Manager, UB Architecture)
Jongmin Shim (Structure Analysis, UB Department of Civil, Structural and Environmental Engineering)
Xiangdong He (Structure Analysis, PhD student, UB Department of Civil, Structural and Environmental Engineering)
Michael Gac (Student researcher, UB)
Bonghwan Kim (Structure Consultant, Skidmore, Owings & Merrill LLP)
supported by:
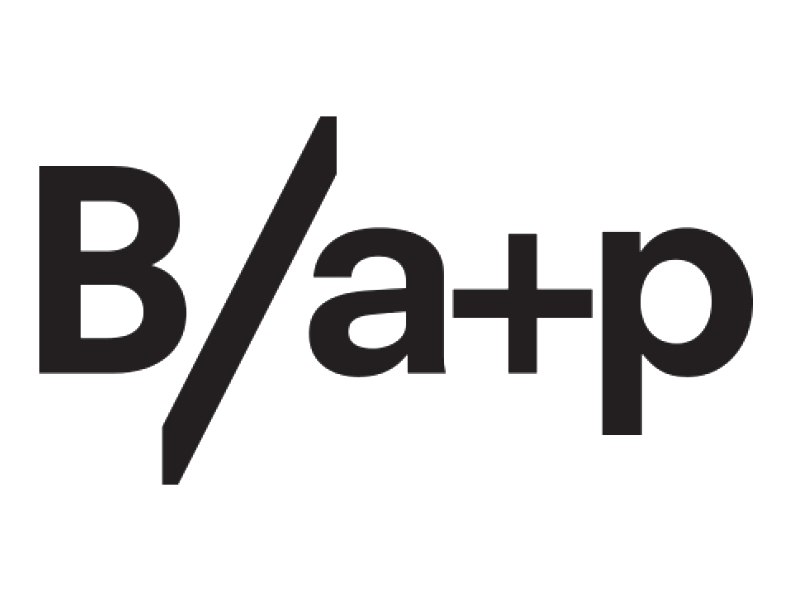


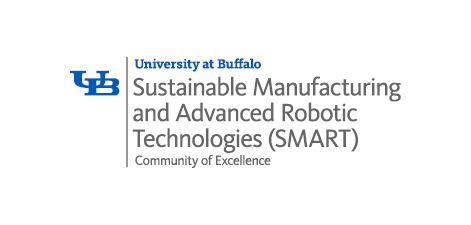